Just how to Create a Reliable Welding WPS: Tips and Best Practices
Wiki Article
Unlocking the Power of Welding WPS: Approaches for Performance and Security in Manufacture
In the realm of manufacture, Welding Treatment Requirements (WPS) stand as the foundation of welding operations, dictating the necessary actions for accomplishing both efficiency and security in the fabrication procedure. Comprehending the details of WPS is vital to utilizing its complete possibility, yet many companies battle to open truth power that exists within these papers (welding WPS). By delving into the methods that optimize welding WPS, a world of enhanced efficiency and increased safety and security waits for those ready to explore the subtleties of this vital element of fabrication
Value of Welding WPS
The relevance of Welding Treatment Requirements (WPS) in the fabrication market can not be overemphasized. WPS function as an important roadmap that lays out the required actions to make sure welds are done consistently and appropriately. By specifying important criteria such as welding processes, products, joint layouts, preheat temperatures, interpass temperature levels, filler metals, and post-weld warmth treatment needs, WPS offer a standard approach to welding that enhances performance, top quality, and safety and security in fabrication procedures.Adherence to WPS assists in achieving uniformity in weld top quality, minimizing the probability of defects or architectural failings. This standardization additionally promotes compliance with market laws and codes, guaranteeing that fabricated structures satisfy the needed safety and security standards. In addition, WPS documentation makes it possible for welders to duplicate successful welding treatments, leading to regular results throughout different projects.
Basically, the thorough growth and rigorous adherence to Welding Treatment Requirements are extremely important for supporting the stability of welded structures, securing against potential risks, and upholding the credibility of manufacture companies for supplying top quality product or services.
Key Elements of Welding WPS
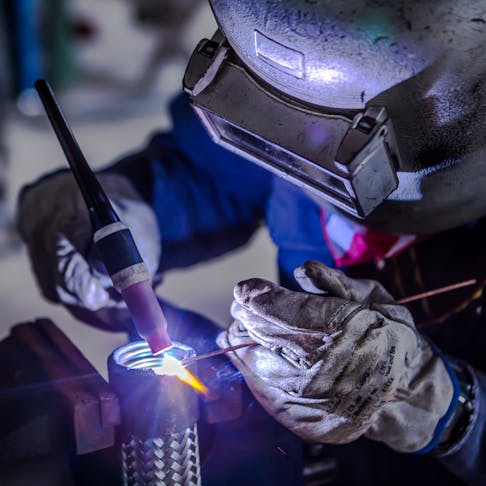
Enhancing Efficiency With WPS
When maximizing welding procedures, leveraging the essential components outlined in Welding Treatment Requirements (WPS) comes to be crucial for streamlining procedures and optimizing performance. One means to improve effectiveness with WPS is by carefully selecting the proper welding criteria.Routinely reviewing and updating the WPS to include any kind of lessons found out or technical innovations can also contribute to performance renovations in welding operations. By accepting the standards established forth in the WPS and constantly looking for ways to optimize procedures, fabricators can attain greater effectiveness levels and premium end outcomes.
Ensuring Security in Fabrication
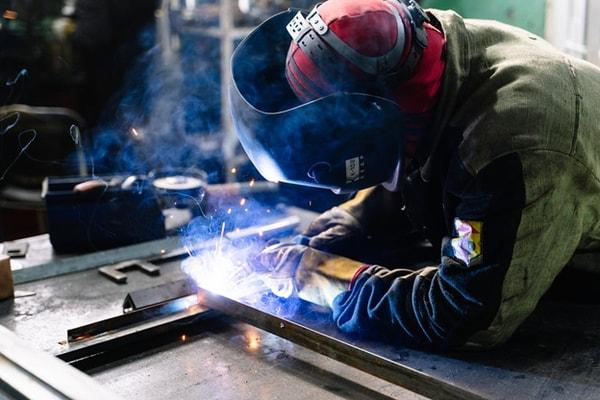
Security procedures in fabrication play an essential duty in securing employees and maximizing functional procedures. Making sure security in manufacture involves a diverse strategy that incorporates different facets of the welding process. One essential facet is the provision of personal safety devices (PPE) tailored to the details dangers present in the fabrication environment. Welders have to be equipped with appropriate equipment such as headgears, handwear covers, and protective garments to reduce dangers related to welding activities.
Furthermore, adherence to proper ventilation and fume removal systems is vital in preserving a healthy and balanced workplace. Welding fumes contain dangerous compounds that, if inhaled, can present severe health risks. Carrying out efficient air flow actions assists to lessen exposure to these harmful fumes, promoting breathing health and wellness amongst workers.
Regular devices upkeep and assessments are also important for ensuring security in fabrication. Damaged equipment can cause injuries and accidents, highlighting the relevance of timely repair work and routine checks. By focusing on precaution and cultivating a society of recognition, construction centers can create a efficient and safe and secure job environment for their employees.
Executing WPS Finest Practices
To enhance functional performance and make sure top quality end results in fabrication processes, integrating Welding Treatment Requirements (WPS) finest methods is extremely important. Picking the websites ideal welding procedure, filler product, and preheat temperature level defined in the WPS is essential for attaining the wanted weld quality. Guaranteeing that certified welders with the necessary certifications bring out the welding procedures according to the WPS standards is vital for uniformity and reliability.Verdict
In verdict, welding WPS plays an important duty in ensuring performance and safety in fabrication procedures. By concentrating on crucial elements, improving performance, and carrying out best practices, companies can optimize their welding procedures. It is necessary to focus on precaution to stop accidents and ensure a smooth manufacturing home procedure. By adhering to these strategies, companies can open the full possibility of welding WPS in their construction procedures.In the world of manufacture, Welding Procedure Specs (WPS) stand as the foundation of welding procedures, dictating the essential steps for achieving both effectiveness and safety in the manufacture procedure. By specifying necessary parameters such as welding procedures, products, joint designs, preheat temperatures, interpass temperatures, filler metals, and post-weld warmth therapy requirements, WPS provide a standard approach to welding that enhances effectiveness, quality, and safety and security in manufacture processes.
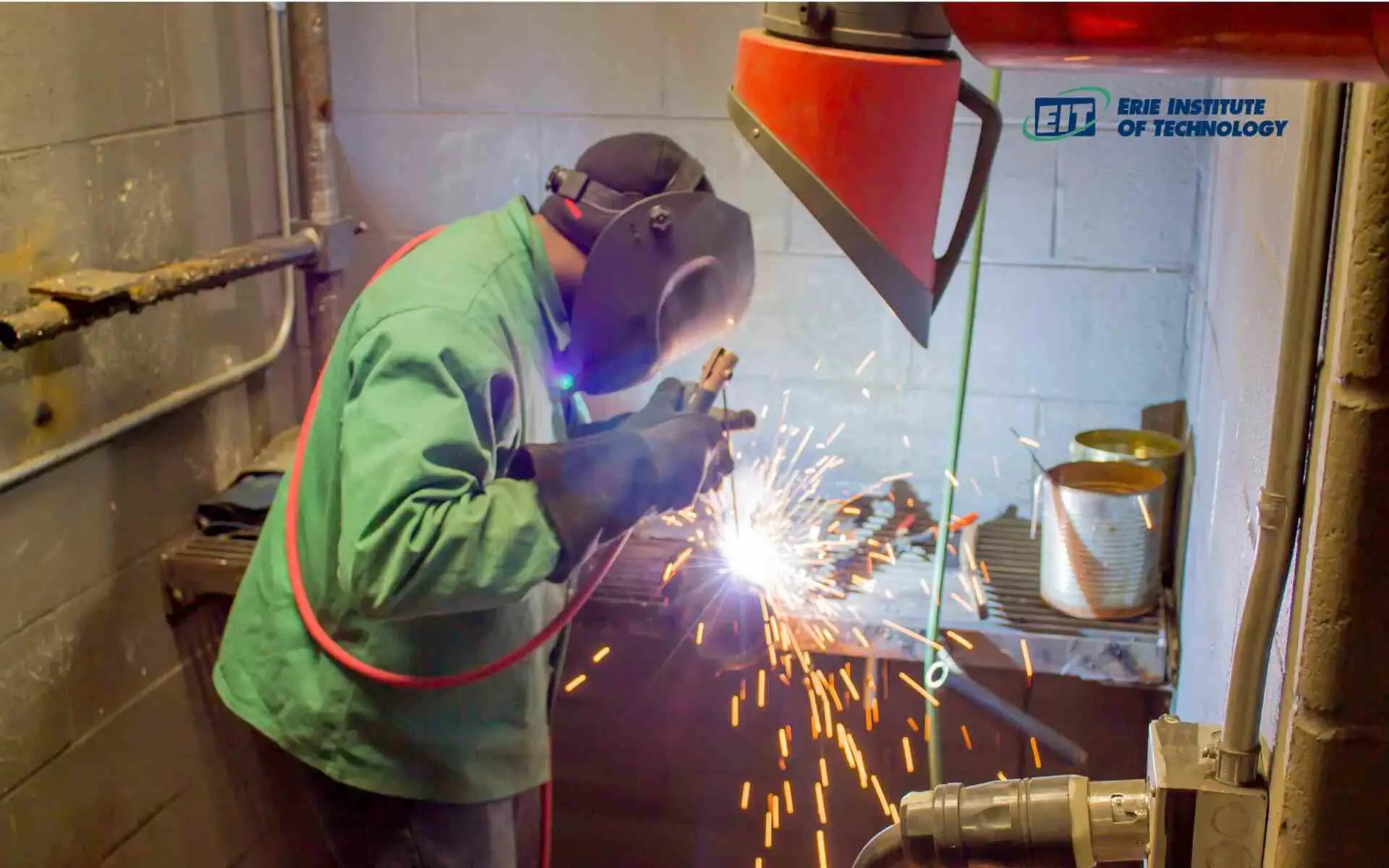
When optimizing welding operations, leveraging the vital aspects outlined in Welding Treatment Specifications (WPS) comes to be necessary for streamlining processes and taking full advantage of productivity. (welding WPS)
Report this wiki page